The Process
Large rolls of FSC® Certified paper, are run through a bath to be saturated with a thermosetting resin, cut into sheets, then stacked into a plywood press where heat and pressure are applied.
Using a thermosetting resin in the manufacturing process, Richlite achieves unsurpassed quality in the finished product and minimizes energy consumption, with no added Urea Formaldehyde. In addition to reduced energy consumption, the resin used has the EcoBind™ designation, due to the fact it is one of the lowest VOC emitters on the resin market. EcoBind™ resins have been formulated to meet or exceed all global emission standards including US HUD, European EMB, and Japanese standards, as well as specifications recommended by the Green Building Council and the State of California.
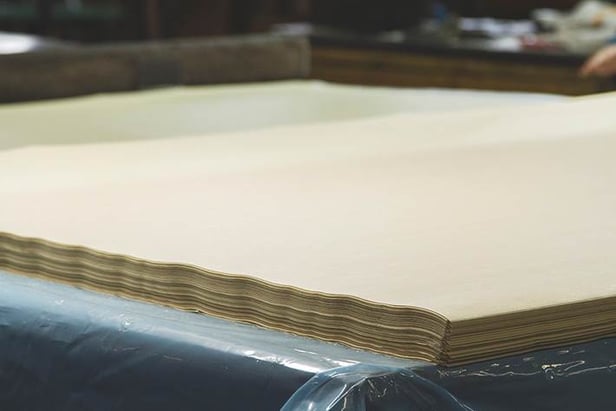
To dilute the solid resin methanol and ethanol are added because they do not create hazardous waste when mixed with the resin. During the processing, excess resin is diverted to a catalytic converter, which heats the resin over a platinum bed to create an energy source (see We™ Technology below).
Because methanol and ethanol are basically alcohols, they burn and evaporate, generating no harmful VOCs that would react negatively with the ozone. This essentially non-emitting process has resulted in a 70% reduction in the carbon footprint of the process since its implementation.
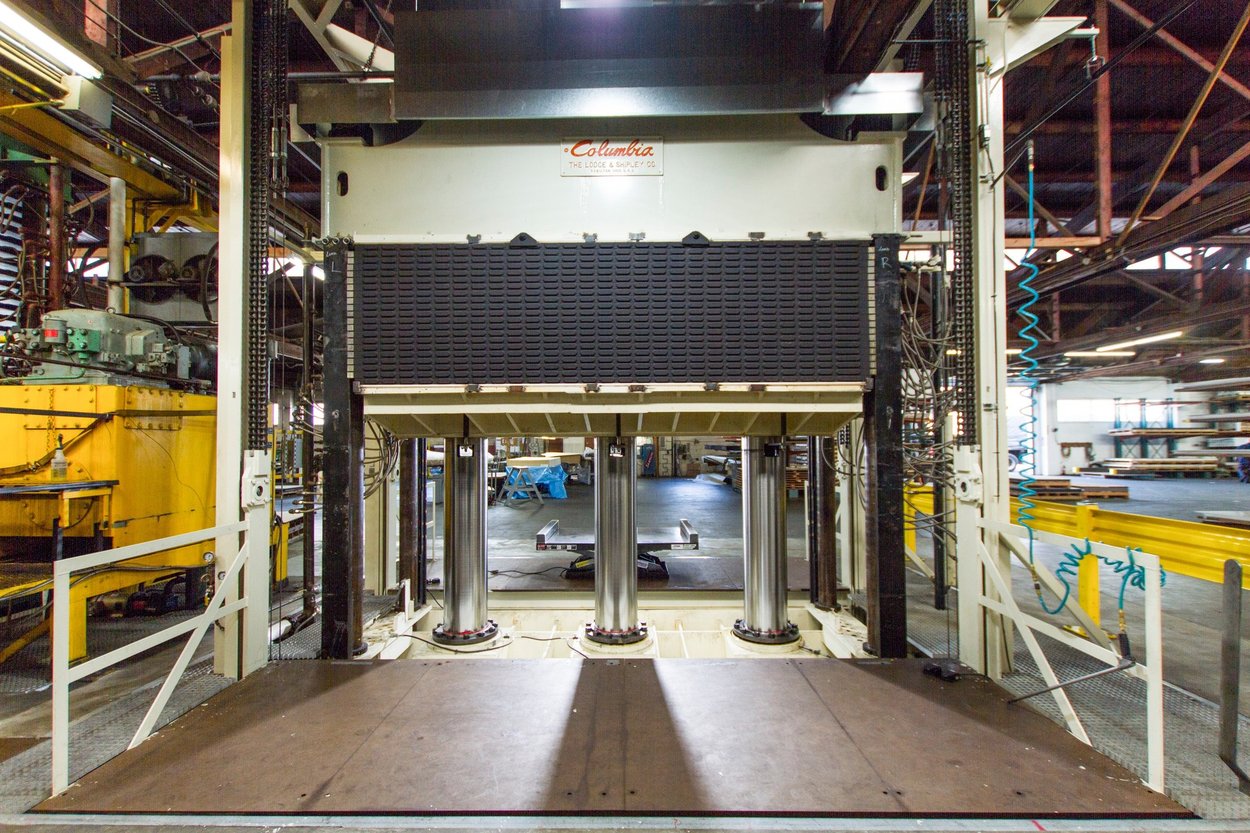
This is a revolutionary manufacturing feat, especially when compared to competing facilities that use reductive thermal oxidizers the size of a large bus to scrub emissions. Because there are so few detrimental emissions to eliminate in Richlite’s manufacturing process, their RTO is the size of a small refrigerator.
While most other facilities use a horizontal drying process, Richlite uses a vertical drying tower to minimize the required airflow by four and a half times. Because the airflow in a horizontal drying process is much greater, competing manufacturers must consume far more energy and create more heat to maintain the necessary airflow. With its one small gas motor, Richlite operates at about 3,500 DCFMs, while most other facilities using four motors require about 15,00 DCFMs. This means Richlite cuts natural gas consumption by more than 80%.
Slowly cooled, the cured panels produce a solid, stable sheet of material. Richlite can be pressed in many various sizes and thicknesses, from ¼” (6mm) to 3” (75mm) thick and sheet sizes up to 5’x12’ (3660 x 1525mm).
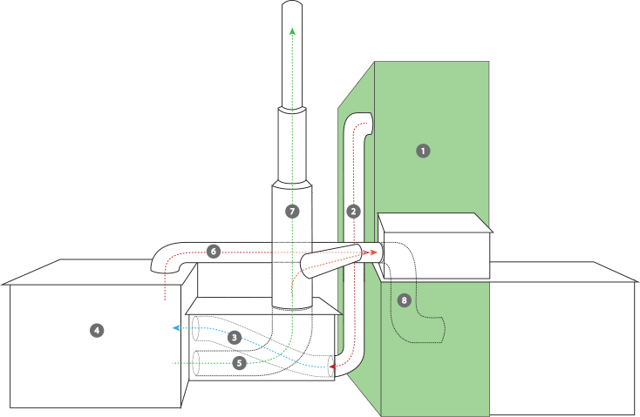
Richlite’s exclusive saturation equipment captures energy from the manufacturing process and recycles it back into the heating system as energy.
- The Vertical Drying Tower is heated to the required temperature, 600°F (315°C)
- Exhaust from the drying tower is captured and cooled to 230°F (110°C) by ambient air
- The cooled exhaust enters the heat exchanger at 230°F (110°C) and is heated to 600°F (315°C) as it passes 900°F (482°C) air (see step 5)
- A catalytic bed destroys 99.99% of VOC’s which generates clean 900°F (482°C) air
- Part of the 900°F (482°C) air is sent back through the heat exchanger, cooling it to 400°F (204°C)
- The remaining 900°F (482°C) clean air is captured and returned to the drying tower – bypassing the heat exchanger
- Before exiting to the atmosphere, 30% of the 400°F (204°C) air is directed back to the drying tower
- Combining the 900°F (482°C) air with the 400°F (204°C) air equalizes to 600°F (315°C), which is recycled into the drying tower, eliminating the need for an additional heat source and creating self-sustaining energy
Video