The design of a new freestanding single family house in McLean Virginia is informed by two specific site conditions. The site was formerly occupied by an existing structure built in 1953 by UVA professor Harry Ormston. The original house included a double height volume family room, a feature that allowed the house to optimize its solar orientation and one that the owners wished to retain. The second feature is a gently sloped and wooded setting that backs up to Langley Fork Park.
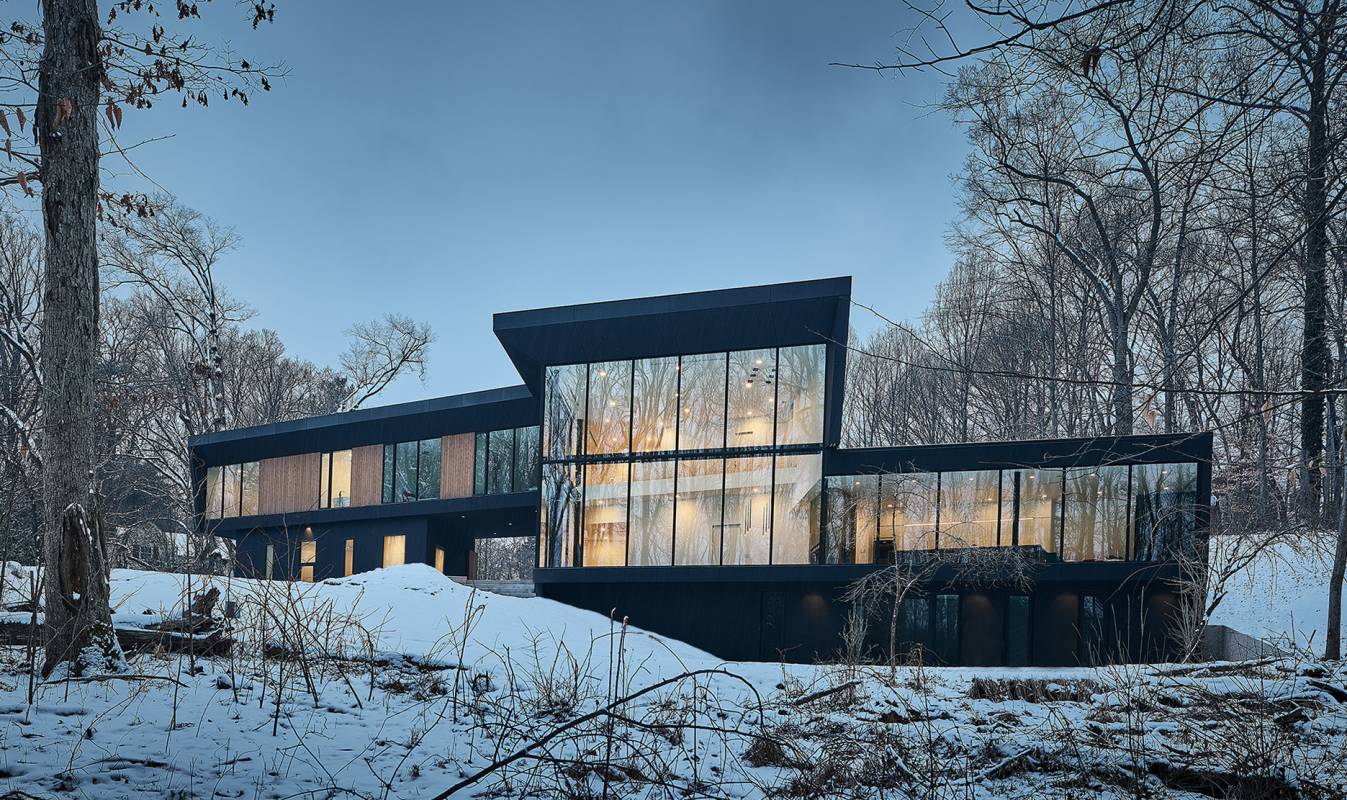
The design for the new house incorporates a double height volume as a "spatial citation" and organizes itself around the views to the wooded back yard. Computer simulations of the solar performance have demonstrated that the new house will self-shade in the summer months, and allow for winter sun to passively condition the family room.
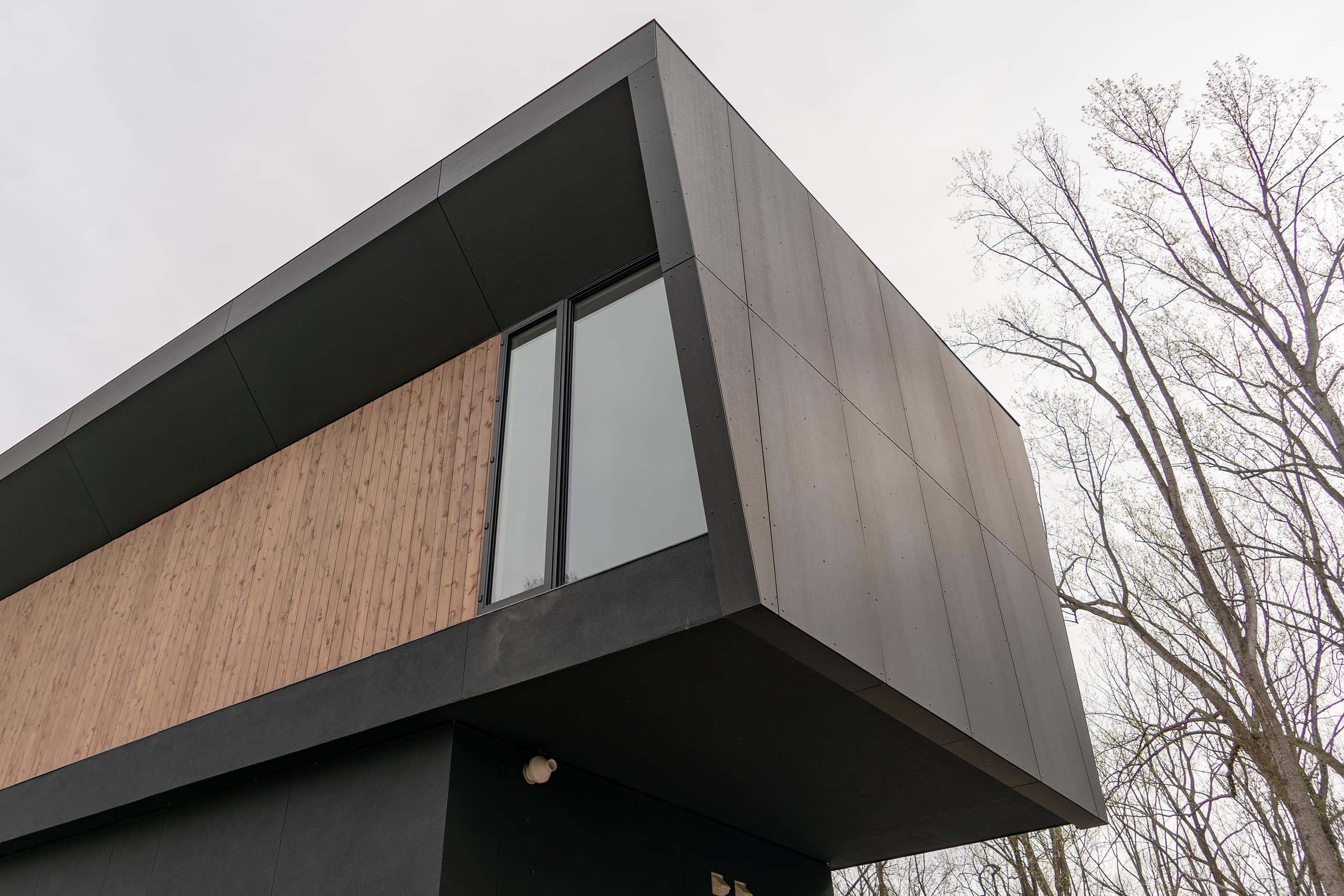
The upper angular soffits and returns, as well as, the north and south upper façade are clad with FSC® Certified Richlite Slate phenolic panels. The complexity of the these “soffit borders” forced our in-house fabrication and install teams to use both delivered pre-cut panel components, as well as, perform onsite field cuts. Because it can be cut with standard woodworking tools, Richlite had its advantages over other exterior panel products such as fiber cement, when it came to onsite measuring and cut-to-fit techniques. At 5/16” thickness, Richlite Slate, is Class A fire rated, color-through, and does not require any maintenance. As it ages, the material will undergo an oxidation process that will yield a rich patina, and if needed, can be pressure washed to remove any grime, dust or dirt. The high tensile strength of Richlite provides industry leading impact resistance. It will not dent, chip or decay even under the most severe weather events. These panels were attached to the building using anodized, black aluminum, hat & J channels and face fastened with black coated SFS stainless steel pan-head screws.
One of the challenges during installation was finding anchor points to mount the extrusions. The original drawings and concept did not call out for a “ventilated” panel facade assembly, and because of this, there was no preliminary plan to sequence the blocking during framing. The site lines on these panels were an integral part of the overall fit-and-finish of the design. Because the blocking was not in place before the sheathing was attached, we needed to mount our extrusions to the sheathing with toggle bolts wherever we could not anchor to a stud. Tedious work at 35’ and cantilevered! At 5/16” thick, Richlite panels should be fastened every 24” on center with a 3/8” reveal between each panel and strategically placed slotted screw holes to allow for seasonal expansion and contraction.
The undulating topography of the site, the height of the soffits and one of the wettest summers on record compounded the difficulty of getting the details correct. However, the ease of cutting, boring and handling along with the overall performance aspects of the Richlite allowed plenty of real time flexibility and onsite adjustments to achieve the proper fit.
This project represents yet another example of how our vertically integrated EcoCuts & Eco Windows & Facades divisions worked closely together to fabricate, deliver and install Richlite panels on a beautifully designed project.
Want to Learn More About Richlite?
We offer an AIA CES Course on Paper Phenolic materials, including Richlite. Click the button below to request a presentation at your firm.